The design idea combines
- Rigidity and Damping
- A low friction unipivot bearing,
- without bearing chatter, but
- with excellent energy transfer to the tonearm base.
You are invited to order this tonearm for a two months test period: info@sambuco.net
If you don’t like it, simply send it back, and you will get your money back.
Table of Contents
Introduction
Tonearm pipe 1
Tonearm pipe 2
Bearing concept
Alignment options
Templates
Design for balance
Anti skating concept 1
Anti skating concept 2
Cartridge_selection
Technical references
Legal information
Blog
Price list & Installation Instructions pdf
Footer
The Tonearm Pipe
This is the core of the matter!
The SAMBUCO tonearm pipe is turned from a rather soft wood: “Sambucus Nigra” or “Elderwood”.
It grows as a natural pipe and has a lot of pores, which widen as the wood dry ages. They will later absorb traditional violine treatments to create a glass-like stiffness.
The permanent and solid combination of soft and hard materials in one functional item creates a resonant-free pipe.
Wood is a natural Constraint Layer Damping („CLD“) design.
Tonearm pipe / 3
Very hard materials (f.ex. ceramic) tend to have discrete high frequency resonances („kling“). Soft materials often sound dull („blob“) You want to hear „tuck“! Short and loud. Loud means good energy transmission, short means good damping.
You are not getting this from any homogeneous material, like metal.
On the SAMBUCO you will notice, that different materials meet at all screws, joints, and contact areas.
Large-area-contacts support wider band energy transfer, not like point contacts, that create instable connections.
The SAMBUCO Bearing
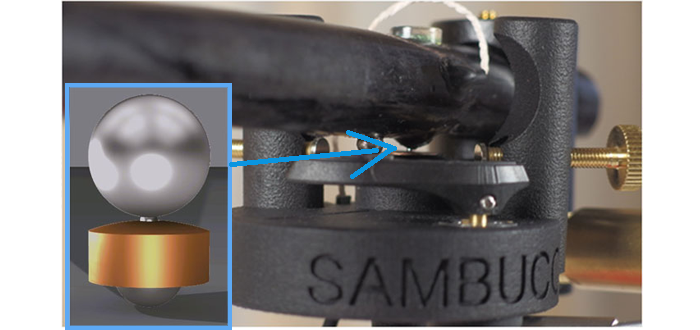
The tonearm bearing is a unipivot concept.
A point contact shows minimal friction.
All energy has to pass through the single bearing point.
High magnetic pressure (1.5 kg) at the contact point and an eddy current damping will keep the bearing contact “silent”. No chatter!

How does the eddy current damper of the bearing work?
There is no resistance to slow (normal) movements (< 1 Hz) of the tonearm.
But high speed vibration (like tonearm resonances) will create higher eddy currents in the copper bearing base.
(The chart is symbolic to visualize the damping concept.)
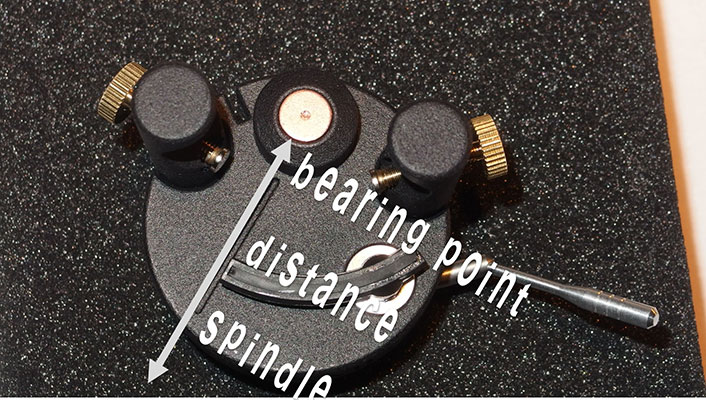
The SAMBUCO offers flexibility for ALL alignments!
The effective tonearm length determines all following steps:
- The distance of the record spindle to the tonearm bearing point, and
- the necessary offset angle.
Mounting the SAMBUCO is very easy: You only have to drill one small mounting hole (diameter: 6 mm) into your record player‘s tonearm base.
Alignment options
Alignment type for tonearm effective length | Spindle – Bearing point distance | Offset angle (degree) |
---|---|---|
„Loefgren“ 240 mm | 224 mm | 22.8° |
„Loefgren“ 300 mm | 287 mm | 18.07° |
„underhang“ the longer, the better. | n.A. => position along a tangent | 0° |

Video link Tonearm Installation
Adjust the offset angle.
There are explanatory videos for the tonearm and for the cartridge Installation
Static and dynamic balance of a unipivot

Imagine the SAMBUCO as a tightrope artist.
- The geometry and mass balance of the SAMBUCO tonearm creates similar momentum forces around the bearing point.
- There are no momentum differences at the needle tip of the cartridge.
- The bearing point is almost on the same plane as the record, so the tonearm shall be immune to warp wow effects.
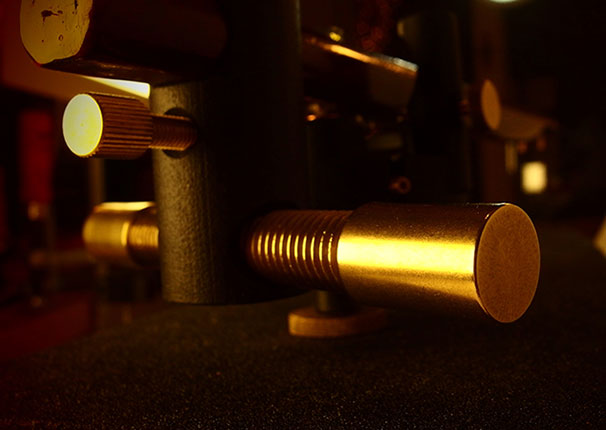
The SAMBUCO counterweight adds more inertia in the horizontal plane.
Usually tonearms offer little left-right inertia to oppose torsional diamond work in the groove.
Therefore the counterweight is positioned 90 degrees against the record groove axis.
Rotating the threaded brass stub allows to fine tune the Azimuth.
The SAMBUCO antiskating solution
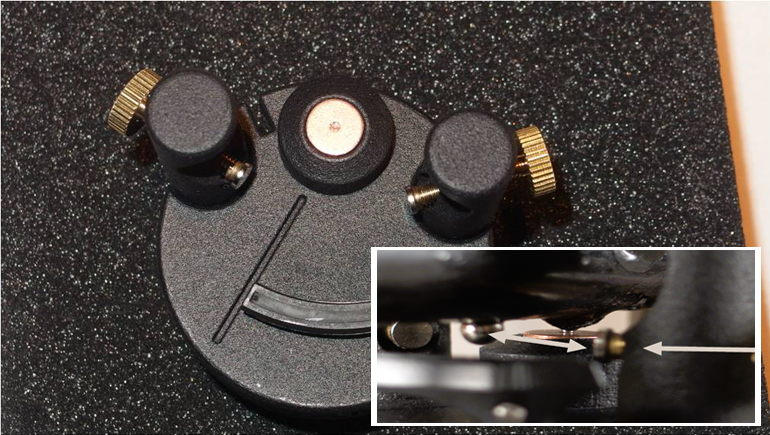
Video link anti-skating final
…is two dimensional and friction-less.
There are two independently adjustable magnets that apply the anti- skating force to the tonearm. The tonearm itself carries a third small magnet that is pulled outwards (outer grooves), and later pushed outwards (inner grooves). All at the bearing level!
By adjusting the distance and the angle of these magnets to each other, you can fine-tune the anti-skating force, “on the fly”.
Anti skating

There is a video that explains the necessary steps:
Video link anti-skating final
Due to the skating drag towards the record centre, there is always enough needle pressure for the left channel modulation (green line).
The applied anti skating force increases the needle pressure for the right channel modulation (blue line). ^Ref.
Eventually a balanced optimum, and the best sound is reached. I start this exercise with a blank record. Fine tuning has to be done by ear.
Cartridge Selection

The SAMBUCO has a medium effective mass.
Due to the low resonance design of the wooden tonearm pipe, and the good energy transfer the question of the effective tonearm-mass is of lesser importance than in older designs.
We have successfully tested a number of cartridges with different compliances:
- on the softer side: Shure V15/III with JELCO SAS stylus, AT95SH (new series).
- on the harder side: DENON 103R, Kiseki Purpleheart (picture).
A “drop of grease” will make a better surface contact and support the all important energy transfer to the arm.
Tonearm Cable

Four gold plated plugs at the cartridge end, and two continuing options:
- A short cable to a standard 5 pole phono plug, to be mounted close to the tonearm base.
- non magnetic RCA cinch plugs at the RIAA preamp input, connected by a 33 AWG high frequency copper litz wire.
Both wiring options are symmetrical.
The fifths wire is for shielding and grounding.
By twisting and gluing these wires together we try to make them mechanically and electrically stable. Only a few centimetres are untreated to keep the cable flexible, where it leaves the tonearm.